Batteries
LG Energy's Ochang plant, Korea's EV cell mother factory
S.Korea vows to help the local battery industry secure competitiveness, earmarking $226 mn to boost the sector
By May 25, 2023 (Gmt+09:00)
3
Min read
Most Read
LG Chem to sell water filter business to Glenwood PE for $692 million
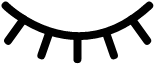
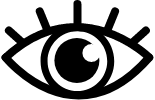
KT&G eyes overseas M&A after rejecting activist fund's offer
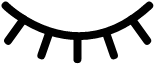
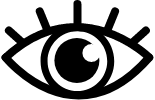
Mirae Asset to be named Korea Post’s core real estate fund operator
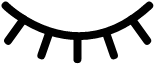
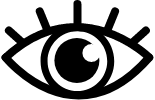
StockX in merger talks with Naver’s online reseller Kream
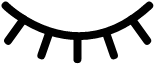
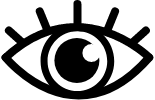
Meritz backs half of ex-manager’s $210 mn hedge fund
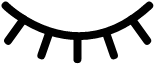
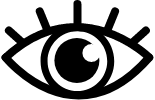
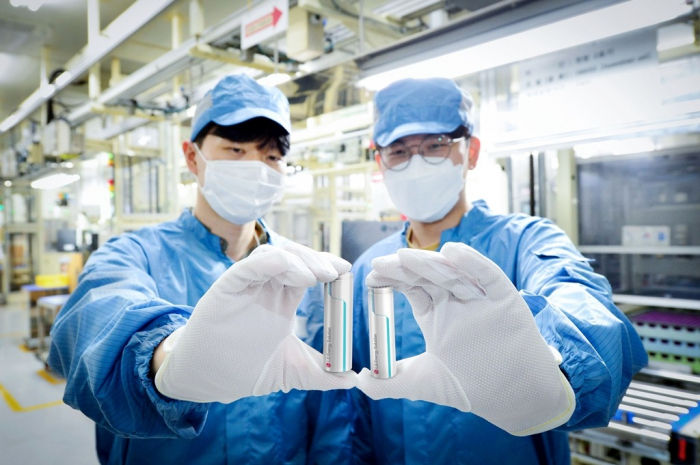
OCHANG, North Chungcheong Province -- LG Energy Solution Ltd., the world’s second-largest electric vehicle battery maker, on Thursday for the first time to outsiders, unveiled its plant manufacturing cells for supply to global EV leader Tesla Inc.
The plant in Ochang, about 130 kilometers (81 miles) south of Seoul, opened in 2004 to produce batteries for electric two-wheelers and laptops but has been mainly manufacturing cells for EVs since 2011.
The production complex named Ochang Energy Plant operates a production line for its flagship 2170 cylindrical batteries, which are supplied to Tesla. An EV of the US company reportedly needs some 4,400 battery cells.
LG Energy recently decided to invest 1.3 trillion won ($1 billion) in the plant to expand its capacity as it became harder to keep up with the surging demand although the company operated the factory with the world’s top production yield at full.
FAST PROCESS
Reporters had to wear cleanroom garments including masks and go through an air shower room before taking a tour of the production line. The air shower room was connected to a battery assembly line, which inserts jelly roll-typed materials consisting of compressed anodes and cathodes on aluminum foils in the prior electrode process into a cylindrical case.
The assembly speed was so fast that it was difficult for reporters to keep up with the process with the naked eye. Cylindrical cases with a diameter of 21 millimeters and a height of 70 mm quickly moved along the production line belt like bullets pouring out of a machine gun. When the belt containing cylindrical cases proceeded horizontally, the equipment worked on them vertically.
During the initial assembly process, injection machines inserted the materials consisting of anodes and cathodes into the cylindrical cases, as well as electrolytes without any error, nodding more than 10 times a second. After that, the components were taken into the welding process that connects the current between the materials in the case and the lid. The welding work took place so quickly that it was invisible.
“The crimp process, which presses the cells' lids to seal them, was also done in an instant,” an LG Energy official said.
VERTICAL INTEGRATION
It took less than five minutes to take a look at the process of the assembly line and listen to explanations from company officials.
Given such a fast process, the production line was estimated to manufacture two or three 2170 battery cells in a second. But the company declined to reveal the output volume or speed of the line as such details may allow its competitors to infer confidential information.
The line was connected with a cathode factory of LG Energy’s parent LG Chem Ltd., which shows off their vertical integration of batteries and raw materials.
LG Energy is building a pilot production line of the so-called 4680 battery in Ochang with an investment of 580 billion won.
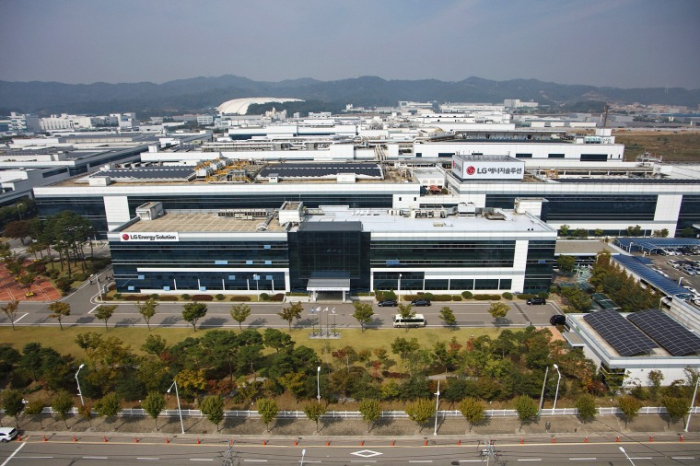
The 4680 type is seen as a game-changer in the battery sector as it is said to increase energy density fivefold and output sixfold compared with the conventional 2170 type, and boost EVs' mileage by about 16%. Tesla CEO Elon Musk said in 2020 that the 4680 battery will determine future competitiveness.
South Korean Minister of Trade, Industry and Energy Lee Chang-Yang, who visited the Ochang plant with reporters, pledged to support the local battery industry.
“K-batteries’ global order backlogs are expected to top 1,000 trillion won this year,” Lee said. “The government won’t spare institutional support to help the industry secure overwhelming competitiveness with a budget of 300 billion won by 2027 for investments in technology and infrastructure.”
Write to Han-Shin Park at phs@hankyung.com
Jongwoo Cheon edited this article.
More to Read
-
BatteriesLG Energy to spend $3.1 bn on 4680 battery plant in S.Korea
Dec 19, 2022 (Gmt+09:00)
1 Min read -
BatteriesLG Energy to invest $451 mn in mass production of Tesla’s 4680 battery cells
Jun 13, 2022 (Gmt+09:00)
3 Min read
Comment 0
LOG IN