Textiles
Korea textiles reborn as eco-friendly, high-tech
Hyosung has dominated the global spandex market with its R&D for 30 years; Kolon focuses on aramid, tire cords
By Dec 08, 2021 (Gmt+09:00)
5
Min read
Most Read
LG Chem to sell water filter business to Glenwood PE for $692 million
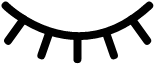
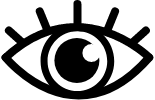
Kyobo Life poised to buy Japan’s SBI Group-owned savings bank
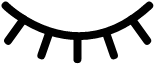
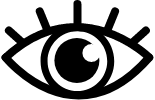
KT&G eyes overseas M&A after rejecting activist fund's offer
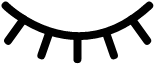
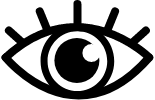
StockX in merger talks with Naver’s online reseller Kream
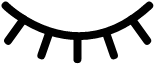
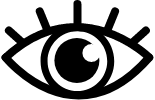
Mirae Asset to be named Korea Post’s core real estate fund operator
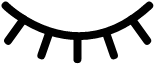
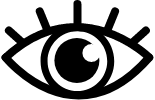
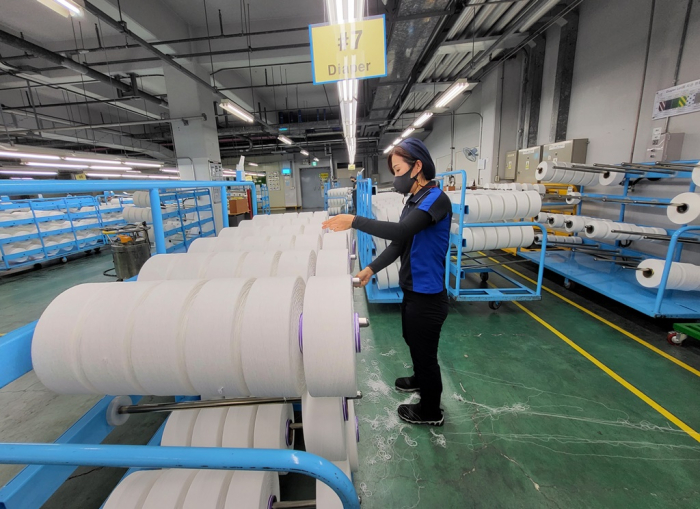
South Korea’s textile sector is reviving as a high value-added growth business with advanced technology. The business, once a leading industry accounting for about 40% of the country’s total exports in the 1970s, had gone into a slump in recent decades alongside the sharp growth in sectors such as electronics and automobiles.
“Some companies may decline, but no industry declines forever,” said a textile industry source.
Hyosung TNC Corp., the world’s top spandex maker, reported 1.1 trillion won ($907.6 million) of operating profit in the first three quarters of the year, about eight times the 136.4 billion won of a year earlier, according to its filing to the financial regulator. The company is likely to become the only textile producer in the country that is expected to log 1 trillion won in operating profit this year.
Kolon Industries Inc., the nation’s first nylon producer, logged operating profit of 249.9 billion won during the January-September period, near triple the 91.9 billion won of a year earlier, thanks to strong demand for tire cords and aramid, the lightweight reinforced fiber with tensile strength five times stronger than iron of the same weight with high heat resistance and low cutability.
RESEARCH AND DEVELOPMENT
South Korea’s textile makers are reaping the rewards of their continuous research and development (R&D) amid the current global economic recovery, industry sources said.
Hyosung took the throne of the global spandex market after three decades in R&D. Spandex production requires high technology as it is difficult to dye yarn and maintain elasticity. The company started developing spandex in 1989, directed by Hyosung Group honorary chairman Cho Seok-rae, and underwent a few years of trial and error before succeeding in making its own spandex in 1992.
It kept investing in R&D on spandex even during the 1997-98 Asian financial crisis despite mounting reluctance to invest in the business that required huge costs.
Kolon kept investing in R&D on high value-added textile products to manufacture aramid, used for 5G mobile communication optical cables, and tire codes for electric vehicle tires.
“The textile sector was able to revive as a next-generation high-tech industry as companies invested in R&D for the future instead of closing down the business,” said another industry source.
TECHNOLOGY AND QUALITY
“This is the only way, to actively develop technology and thus secure good quality for survival in the textile industry,” Lim Gyu-ho, Hyosung’s chief product officer, tells his staff.
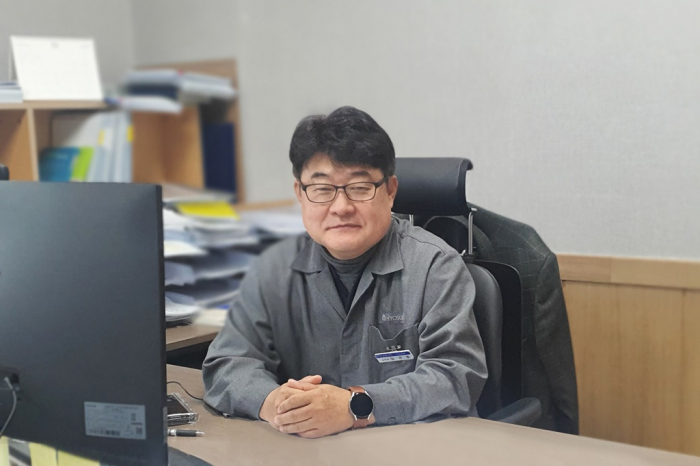
Lim, who joined the company, formerly known as Tongyang Nylon, in 1991, participated in the spandex R&D in the following year.
“It is most important to develop differentiated technology for an industry that once was regarded as a declining sector,” Lim told The Korea Economic Daily at the company’s plant in Gumi, South Korea. He is now leading the development of Hyosung’s new products.
When he joined the company, it was a big challenge to produce spandex fibers for velvet fabrics, Lim recalled.
“Now, the challenge is to make softer spandex that is good for skin and easier to dye with heat resistance, as well as biodegradable spandex,” he said. “I realized how advanced the technology has become when I look at the products we have manufactured over the last 30 years.”
Hyosung is the only South Korean company that produces its own PTMG, a key raw material for spandex. It makes various types of PTMG to manufacture differentiated spandex.
“It is essential to secure good PTMG for good spandex,” Lim said. “It took five to six years only for R&D on raw material production.”
He sees risks on growing competition with Chinese textile makers. They have been focusing on mass-produced textiles rather than value-added products, but they are narrowing the technology gap with South Korean companies.
Lim said R&D is key to winning the competition.
“We are selling textiles with high quality and better productivity technology at prices 10-30% higher than Chinese products,” Lim said. “We will try to stay at the top since products with more spandex are popular despite the high prices.”
HIGH QUALITY, BETTER FUNCTION, ECO-FRIENDLY
Hyosung’s domestic peers are also focusing on textiles with better quality and advanced functions that are used in high-tech industries.
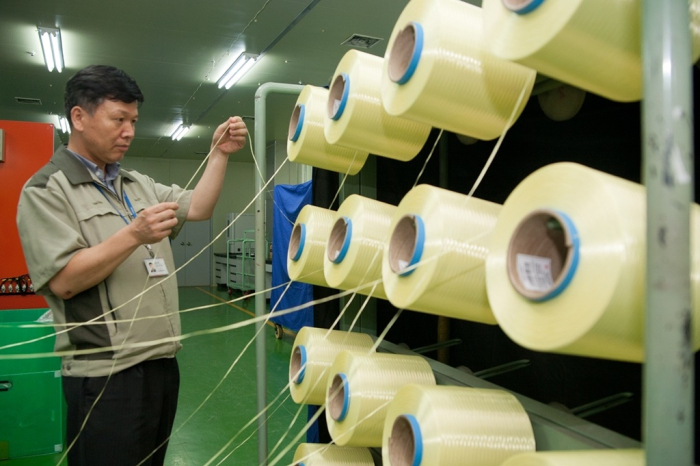
Kolon plans to double its aramid production capacity to 15,000 tons a year by 2023 from the current 7,500 tons with an investment of 230 billion won.
Taekwang Industrial Co., the first South Korean company that commercialized spandex in 1979, is now developing eco-friendly textiles. In the second quarter, the company developed spandex made by recycling plastic waste. It is testing the recycled spandex to be used to make bags and underwear for women and aims to decide on its commercialization by year-end.
“The market for recycled spandex is expanding to fabric for shoes and t-shirts,” said a Taekwang source. “We plan to further expand eco-friendly textile products.”
The company has been developing technology with other companies at home and abroad to extract fibers from low-quality plastic waste.
Huvis, a joint venture between SK Chemicals Co. and Samyang Corp. to produce fiber materials, is working on smart textile products that are capable of detecting electrical conduction, heat generation and bio-signals.
Write to Jeong Min Nam and Jung-hwan Hwang at peux@hankyung.com
Jongwoo Cheon edited this article.
More to Read
-
Business & PoliticsTrump Jr. meets Korean business chiefs in back-to-back sessions
Apr 30, 2025 (Gmt+09:00)
-
Korean chipmakersSamsung in talks to supply customized HBM4 to Nvidia, Broadcom, Google
Apr 30, 2025 (Gmt+09:00)
-
EnergyLS Cable breaks ground on $681 mn underwater cable plant in Chesapeake
Apr 29, 2025 (Gmt+09:00)
-
Business & PoliticsUS tariffs add risk premium to dollar assets: Maurice Obstfeld
Apr 29, 2025 (Gmt+09:00)
-
Comment 0
LOG IN