Hidden Champions
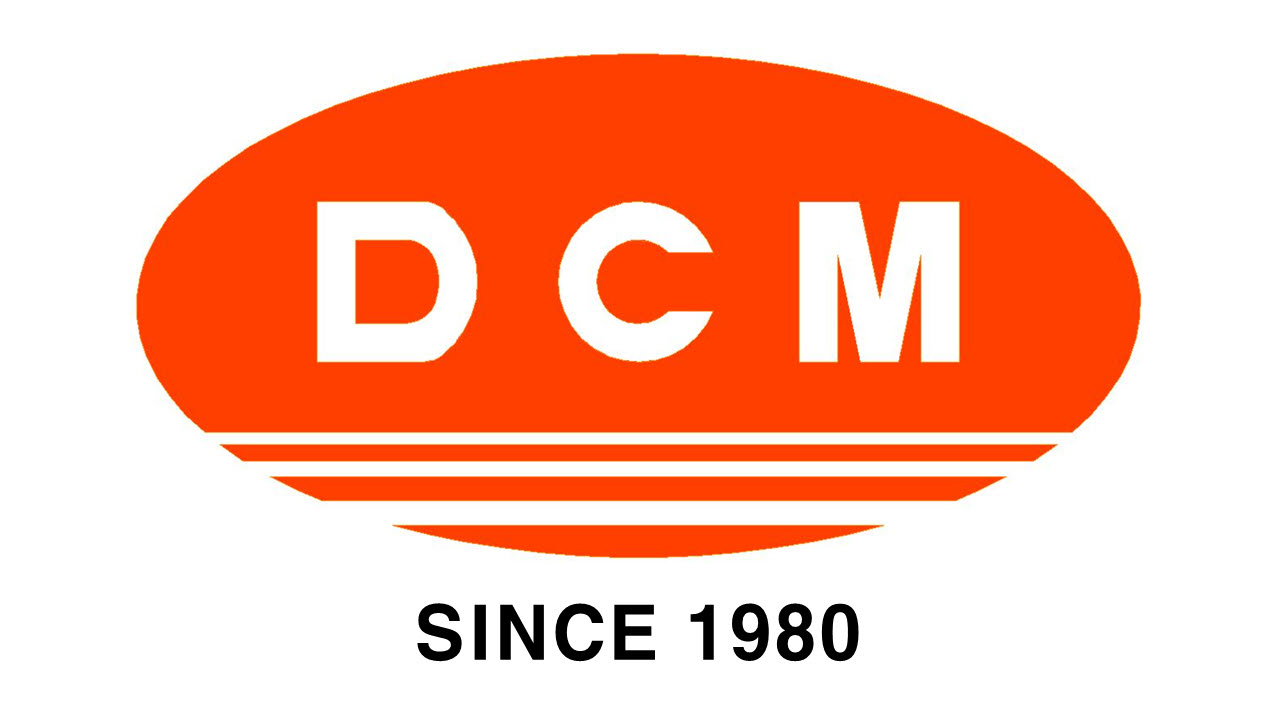
DCM has developed and manufactured surface treatment equipment and related products for a global clientele for over four decades. Founded in 1980, DCM has grown to specialize in manufacturing mass-finishing machinery as well as lapping and polishing machinery.
- Story
- Data
Four decades of providing finishing touches to precision machinery
DCM aspires to be a chameleon in meeting different finishing needs
DCM has developed and manufactured surface treatment equipment and related products for a global clientele for over four decades.
Founded in 1980, DCM has grown to specialize in manufacturing mass-finishing machinery as well as lapping and polishing machinery.
The unlikely hero that rescued the domestic metal finishing machinery industry back then is a household name in South Korea.
In the late 80s, then Hyundai Motor Group Chairman Chung Ju-yung ordered the conglomerate to use made-in-Korea parts and equipment to build fully domestic-made cars, which provided a turning point for the fine machinery maker.
The Ansan, Gyeonggi-based company continues to evolve, producing advanced finishing machinery at the leading edge of industry trends.
Contents
-
[Corporate history] Since 1980
South Korean precision machinery maker DCM Co. was founded to make domestic production of precision machines possible and reduce the rate of errors,” according to its Founder and Chief Executive Officer (CEO) Lee Jae-seo.
Showing typical Korean humility, Lee attributes the long-running success of his company to the robust business climate of the 1980s.
“In the early 80s, you could be in any business sector in Korea and make money just by taking it one step at a time,” the 68-year-old said.
In an interview with The Korea Economic Daily at DCM headquarters in Ansan, Gyeonggi Province, Lee said the concept of a career track was a luxury for a countryman just trying to make ends meet.
Lee was born to a hard-working farming couple in Dangjin, South Chungcheong Province, and was only able to complete elementary school in a normal timeframe, though he later obtained his high school general equivalency diploma.
Nowadays, he is pursuing a doctoral degree after completing a graduate program at the state-funded Tech University of Korea, formerly known as Korea Polytechnic University.
“I was looking for a product to support my family with after getting married, making something that can replace an import appealed to me,” said Lee.
Founder and CEO Lee Jae-seo -
[Growth trajectory] Help from Hyundai
In the late 70s and early 80s, most metal finishing machines in Korea were imported. At the time, Korean companies would import so-called mother machines — those used to build other machines — from Japan and Germany.
The finishing machines use spinning tools to carve complex shapes out of roughly-cast pieces of metal. The results include molds used for die casting, gears for transmissions, and cases for smartphones.
The Korean-made finishing machines were mostly modified versions based on the imported mother machines. As such, the original mother machines, which were not Korean-made, were still preferred at home and abroad.
“DCM contributed a lot to the domestic economy by participating in exhibitions abroad and attracted $2.3 million worth of bids in the book-building process," said Lee, adding that he feels proud to have succeeded in the domestic production of the milling machines and to export them around the globe.
Receipts for orders and for advertising in Korean newspapers in the 1990s (Graphics by Sunny Park)
Lee said the unlikely hero that rescued the domestic metal finishing machinery industry was – and still is – a household name in Korea.
In the late 80s, then Hyundai Motor Group Chairman Chung Ju-yung ordered the conglomerate to use made-in-Korea parts and equipment to build fully domestic-made cars,” Lee said in describing the turning point for the precision machinery industry.
Chung reportedly invited himself to the prime minister’s office to demand the government's assistance in building a fully domestic car, according to two-time Prime Minister Kim Jong-pil’s account in a newspaper op-ed piece.
DCM was one of the beneficiaries of the Hyundai Group founder’s personal crusade to bolster the domestic manufacturing ecosystem.
Lee said he vividly recalls delivering vibratory barrel-finishing machines and continuous-flow vibratory finishing machines in 1987 to Hyundai Motor's Ulsan plant, to this day the world’s largest car-making plant. -
[Overseas expansion] China plant
In addition to its Ansan headquarters, the company also has a factory in Qingdao, a major port city in China's eastern Shandong Province.
Qingdao DCM Co. was founded in 2000 and as Lee explains, the company enjoyed brisk sales from the plant right from the start.
Most of the company’s "3D" or dirty, difficult, and dangerous work such as metalwork and welding has been relocated to China.
The Korea location retains only a small cadre of personnel for producing electric controllers, R&D activity, and trading.
Thus, the Qingdao plant focuses on manufacturing while the Ansan plant south of Seoul is focused on final assembly and R&D.
"We have to outsource these activities [abroad] because young people in Korea refuse to do it,” the CEO lamented.
However, the fate of the China location is unclear due to China’s growing technological prowess which could lead to competitive relationships between Korean companies and their former Chinese manufacturing plants.
Many Korean companies have begun to untether themselves from their plants in China and DCM is considering doing the same. -
[Corporate structure & revenue stream] Beyond Korea
The Korea headquarters has around 20 people, five of whom are engineers, and the remainder are involved in international trade and customer service.
Additional office staff handles the control systems for both Korea and China.
The company's annual revenue hovers between $3.5 million and $4.5 million from domestic sales and another $2 million from abroad.
The company is thinking big as it aims to raise its combined revenue to above 30 billion won or $23.6 million.
As the CEO noted, until the early 1980s, Korean companies imported mother machines and automation systems from Germany and Japan.
But in 1984 the balance began to shift as DCM exported its first batch of mother machines to Japan, then expanded to the US the following year.
Today, DCM exports to 14 countries: the US, Canada, Australia, Japan, Mexico, Guatemala, Hungary, Poland, Indonesia, Singapore, India, Vietnam, Taiwan, and China.
DCM’s first foray into the US market was in 1985, the same year it began exporting its barrel-finishing machines to the country. With support from the Korean government, the company showcased its products at the Los Angeles Convention Center that year.
Nowadays, the company’s agent in charge of OEM business for the US is based in Minneapolis. -
[Products] Finishing touches
Broadly speaking, a finishing machine is a mechanical device running on forms that are used to strike off and shape concrete surfaces.
DCM manufactures five kinds of finishing machines as well as a lapping and polishing machine. Apart from machinery, it also sells finishing and polishing media, separators, and more.
One of its signature products is a centrifugal disc-finishing machine.
Centrifugal disc machines work by using a polyurethane-lined drum with a disc at the bottom to create a rolling motion with the parts and media. The rotation of the disk pushes the part and media upward while providing rotation. This continuous rolling and flow of the part against the media provide highly efficient deburring and finishing.
Among its many other noteworthy machines are centrifugal barrel finishing machines and vibrating finishing machines.
Because the finishing process requires cleaning, DCM provides an all-in-one process. Besides machines, the company also distributes dryers and wastewater treatment systems.
However, the focus is still on the machines because companies that use DCM machines must use DCM-made consumables and cleaning agents to ensure long-lasting performance.
The four main products for DCM -
[Value proposition] Conglomerate clients
The company asserts that its technology is competitive with its top-tier counterparts, namely Rösler Oberflächentechnik Gmbh (Rosler) in Germany, and the US companies of Almco Inc. and Tipton Machinery Company.
And DCM machines are highly price competitive than their better-known competitors' products.
Not surprisingly, the company is a steady supplier to vendors to Korean conglomerates such as Samsung Electronics Co., Hyundai Motor Company, and Hyundai Transys.
It also supplies surface treatment machinery for making aircraft parts and propulsion systems to Hanwha Aerospace, Korea’s only aircraft engine manufacturer.
Orders from Hanwha are forecast to grow after the company's plant being built in Vietnam, goes online.
DCM has already received orders from EV battery die-casting makers with half of the contract already paid to cover R&D.
Die casting is a metal casting process that involves forcing molten metal into a mold cavity under high pressure. The cavity is created using two hardened tool steel dies that have been machined into shape and
work in a way similar to and injection mold during the process.
-
[Future growth engines] EV batteries, golf balls, costume jewelry
The scope of objects that the DCM polishing machines can apply the deburring process to is nearly unlimited, the company says.
Deburring and polishing is a crucial step in many manufacturing processes that removes the build-up of burrs and other imperfections from finished surfaces. It must be completed before other processes such as powder coating and electroplating can proceed.
The process is necessary for making a range of everyday products, from eyeglass frames and nail clippers to dental implants.
The company is betting on three new business areas to generate future revenue: parts for electric vehicles, dimples for golf balls, and deburring for fashion jewelry.
Sectors that see growing demand for surface finishing: EV batteries, golf balls, and imitation pearls (Graphics by Sunny Park)
EV batteries
DCM will launch a new line of spiral-flow barrel finishing machines in 2023 to be used for treating the surface of EV battery parts estimated to be worth around $300,000 per machine.
Once fully charged, an EV battery can power a vehicle up to about 600 km.
But battery makers are working on batteries that can increase the coverable distance to as far as 1,000 km on a single charge.
As these more powerful batteries change in size, the company forecasts continued demand for new machines used to treat the surfaces of different-sized battery parts.
Golf balls
The rising popularity of social outdoor sports in response to the social distancing measures put in place during the pandemic boosted the demand for golf ball finishing machines.
Companies that saw surges in revenue include Massachusetts-based golf equipment maker Titleist, whose parent company is Fila Korea, and Seoul-based golf ball maker Volvik.
A golf ball has from 250 to 500 dimples on it, all of which must be symmetrical.
DCM manufactures centrifugal disc finishing machines that put the finishing touches on golf ball surfaces before the painting process.
All golf ball makers need dimple polishing machines. Whether it is a set of two golf balls used at practice ranges, sets of three balls most commonly seen, or premium six-piece constructions, all require finishing before being painted.
A centrifugal disc finishing machine does injection molding for balls to clean up the balls' parting line.
Costume jewelry
Finally, DCM is also betting on the rise of middle-class consumers in developing countries and their demand for fashion jewelry.
The finishing machines are used to treat the surfaces of parts that take spherical shapes in the medical device, jewelry, and semiconductor parts industries.
For example, when making imitation pearls now popular across Africa, the core is made of plastic and covered with paint made with powdered pearls.
The DCM machines handle the deburring and drying of the plastic — and sometimes pewter — cores before being painted to resemble real pearls or 14K gold jewelry. -
[Challenges] Hiring challenges, shipment delays
There are two main challenges to the company’s growth.
The first is finding and retaining people who want to work in the manufacturing sector.
Nowadays, engineers and researchers under the age of 40 show a strong preference for working in software development, not hardware.
“Young people do not want to work for money these days and prefer to have a work-life balance,” Lee said, adding that it’s nearly impossible to find welders in their 30s or younger.
The second bottleneck is disruptions to logistics due to the frequent trucker strikes in Korea and the US this past year.
Unionized truckers in Asia’s fourth-largest economy voted to end their strike in early December, hit by waning public support and an unflinching stance by the Yoon Suk-yeol administration. The truckers held an eight-day walkout last summer.
Meanwhile, shipments to the US have been held up for up to three months once arriving on the mainland due to trucker protests, Lee explained. -
[Going forward] Corporate structure and future trajectory
Instead of adding more divisions at its headquarters, DCM plans to add more affiliates through M&As.
"While many of our clients want us to also offer machinery that takes care of the steps before deburring and polishing, our strategy is to focus on what we do best," Lee said.
The goal is to expand the number of uses for deburring solutions rather than manufacturing the machines needed in the earlier steps of production.
By Jee Abbey Lee (jal@hankyung.com)